The
ELTROPULS process is completely reproducible.
Process
parameters are microprocessor controlled
and optimised throughout the heat treatment
cycle, to produce the best metallurgical
results. Parts can be heated in the shortest
possible time, in vacuum, by radiation or
in an inert atmosphere, with natural or
forced convection. Even the most complicated
programs can be easily reproduced.
After
reaching the end of the heat and soak steps,
the part can be automatically cooled.
The
cooling method can be selected to meet the
requirements of the part - slowly, in a
vacuum to insure freedom from distortion,
or more quickly, in an inert atmosphere
with natural or forced convection, for high
throughput and productivity.
Passivated
surfaces can be activated by sputter cleaning.
Critical
chemical reaction kinetics are improved
by sputtering.
The
ELTROPULS plasma power is automatically
limited to just the amount necessary
This
ensures uniform temperature of the
parts and allowing loading of a maximum
number of parts in the furnace. Using the
smallest amount of power for the process
prevents overheating of thin sections (as
occurs with technologies lacking pulse duration
and duty-cycle control). This guarantees
consistent nitrided layers whether full
loads or partial loads are run.
Load
size is not critical.
Parts
with different geometries can be treated
at the same time. Cold-Start to Cold-Stop
processing permits small batch operations
without utility cost penalties.
The
low consumption of electrical power, process
gases and cooling water
ensures
a beneficial surface modification operation
at minimum expense.
All
of these features permit high parts production
with the best metallurgical quality.

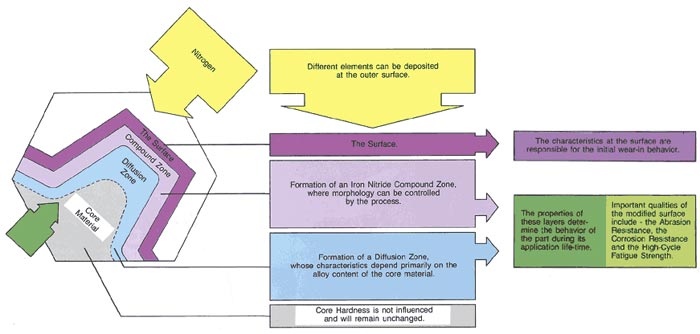
The
surface treatment process with pulsed plasma
offers unique advantages:
- With the ELTROPULS
process all possible nitrided layers can
be created.
- The ductile g' layers are normally 2 to 8 mm
thick and the e layers, which also have good corrosion resistance,
have a thickness of up to 20 mm. Both layer types display good wear resistance.
- Optimal layer thickness and type can be tailored to meet specific application
requirements by the ELTROPULS process.
- For dynamic highly loaded parts or tools, a think g'
layer or compound-free layer with high
compressive stresses is recommended.
- The properties of nitrided
layers can be further improved with post
treatments.
- Post oxidation gives
the parts a decorative appearance and
improves the corrosion resistance.
- Hard coating enhances
hardness and wear resistance and reduces
friction.
- The ELTROPULS-process
can produce all of the mentioned layers
at low cost with precise repeatability.
- Optimal shape control
is guaranteed to prevent postnitriding
machining.

|